Share this
4 Ways Direct Laser Engraving Aids Flexo Printing Quality & Efficiency
by Luminite on Aug 9, 2022 12:43:00 PM
You likely recall the flexo printing evolution through the years in response to pressures from the economy and demand. As industries produced more, they required more packaging and more stylistic choices. And as they’ve required more packaging, they’ve required higher-quality printing to make their products more identifiable and promotable.
So flexo industry thinkers have continually returned to the drawing board to increase productivity and quality:
- More press uptime
- Higher speeds
- Continuous print
- Fewer printing defects
- Less time troubleshooting
- Less waste
- Brighter colors
- More diverse capabilities
The result? Direct laser engraving (DLE) elastomer sleeves. There are four key ways DLE has changed the game in both flexo printing quality and efficiency.
Improving Flexo Printing Quality With Direct Laser Engraving
Despite some lag time being adopted in the North American flexographic market, DLE has emerged in response to the prevalence of in-the-round (ITR) elastomer sleeves. They’re produced by removing non-printing areas through laser ablation.
Washing down photopolymer usually involves solvents that can be harmful to users and the environment if not disposed of correctly. Elastomer blends don’t require such solvents, and in most cases are cleaned up with a water- and soap-based cleaning detergent after the laser-ablation process.
For decades, flat photopolymer printing plates dominated the flexo market in North America. But in some applications, flat plates yield costly flexo printing quality control issues like press misregistration. ITR sleeves have become the solution for a seamless, continuous print.
Here are some of the benefits:
1. Increased Production Speed
There are far fewer steps required to make an ITR elastomer sleeve press-ready, as compared to conventional photopolymer plates, digital photopolymer plates, and simple laser-engraved plates. Fewer steps mean fewer chances for error.
Elastomer sleeves’ thickness and durability allow them to print continuously 2-4x longer than photopolymer plates. You won’t need to buy or make multiple plates for long jobs or repeated short jobs, which typically require multiple cleanings and remounting.
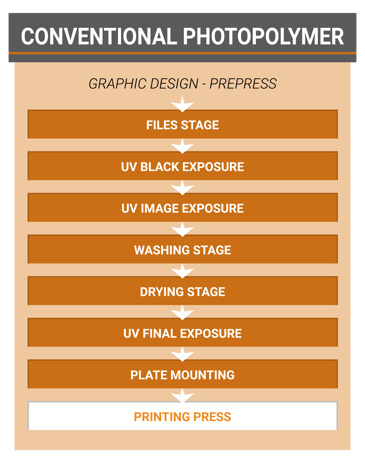
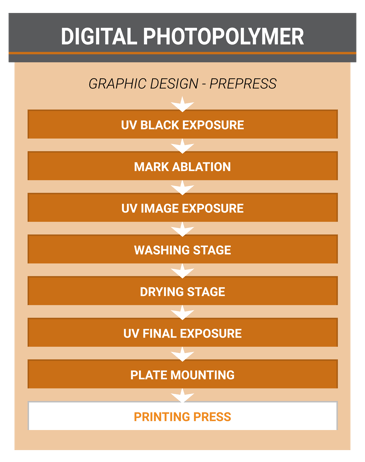
Additionally, the process requires no extra labor and mounting materials. “Load-N-Lok” and you’re good to go.
2. Fewer Registration Issues
Misregistration is one of the most common flexographic printing defects encountered in the industry. Quite often, it’s a problem of misalignment. But it also could stem from press mechanics or plate lift. Sleeves can be notched to align with each other as they’re engraved to achieve optimal registration.
Laser-engraved sleeves manufactured in the round don’t experience plate lift. You’ll also have fewer issues with cylinder bounce or uniformity.
3. High Definition and Clarity
Laser engraving technology can create some of the most intricate, detailed images possible. Here are some of the high-def capabilities:
- Depths up to 0.125″
- Embossing 2D & 3D
- Text point size as small as 0.75 for a basic non-serif font
- Screens for gradients, vignettes, and 4-color process up to 175 lines
- Minimum line weight of 0.001″
- Multiple engraving profiles
What’s more, engraved elastomer sleeves are resistant to harsh chemicals and abrasion. There’s very little chance for image skewing from wear over time.
4. Reduced Waste and Related Costs
Without registration issues and vulnerability to wear and tear, DLE elastomer sleeves don’t create much-wasted substrate. There’s simply no need to waste ink printing costly lengths of the substrate, making adjustments, and testing more to get the quality you need.
This can also streamline your printing operation and limit labor costs. Your employees should be able to finish projects more quickly and move on to other tasks.
Direct Laser Engraving Achieves Quality & Efficiency
The success of your flexo printing operation hinges upon quality and efficiency. Now, with direct laser-engraving technology and ITR elastomer, you can achieve high-end print results in a fraction of the time.
With a great cleaning and maintenance regimen, your flexo sleeve investment could last a very long time.
Let’s work toward printing perfection. Can we help? Call (888) 545-2270.
(Editor's note: This article was originally published in February 2018 and was recently updated.)
Share this
- Flexographic Printing (81)
- Image Carrier (28)
- Elastomer sleeves (27)
- Ink Transfer (25)
- Quality (22)
- Flexo sleeve (20)
- News (18)
- printing defects (18)
- flexo printing defects (17)
- sustainability (13)
- Flexo Troubleshooting (12)
- Ink (12)
- Digital Printing (10)
- Flexo 101 (10)
- Flexo Inks, (9)
- Anilox (7)
- Blister Packaging (7)
- Cost (6)
- print misregistration (6)
- regulations (6)
- Corrugated Printing (4)
- pinholing (4)
- "Tradeshow (3)
- Digital Flexo (3)
- Gravure Printing (3)
- Insider (3)
- Load-N-Lok (3)
- Wide Web (3)
- direct laser engraving (3)
- flexo-equipment-accessories (3)
- gear marks (3)
- halo (3)
- testing (3)
- Narrow Web (2)
- bridging (2)
- feathering (2)
- filling in (2)
- mottled image (2)
- pressure (2)
- Labelexpo (1)
- dirty prints (1)
- doughnuts (1)
- embossing (1)
- kiss impression (1)
- October 2023 (2)
- September 2023 (1)
- August 2023 (1)
- July 2023 (3)
- June 2023 (1)
- May 2023 (5)
- April 2023 (1)
- March 2023 (2)
- February 2023 (1)
- January 2023 (3)
- December 2022 (1)
- October 2022 (3)
- September 2022 (2)
- August 2022 (2)
- July 2022 (3)
- May 2022 (1)
- April 2022 (4)
- March 2022 (2)
- February 2022 (5)
- January 2022 (7)
- December 2021 (1)
- November 2021 (3)
- October 2021 (2)
- September 2021 (1)
- August 2021 (1)
- July 2021 (3)
- June 2021 (1)
- May 2021 (4)
- April 2021 (4)
- March 2021 (4)
- February 2021 (2)
- December 2020 (1)
- November 2020 (1)
- October 2020 (2)
- September 2020 (1)
- August 2020 (3)
- July 2020 (2)
- June 2020 (3)
- May 2020 (1)
- April 2020 (1)
- November 2019 (3)
- October 2019 (1)
- August 2019 (1)
- July 2019 (1)
- April 2019 (1)
- March 2019 (1)
- January 2019 (1)
- October 2018 (2)
- August 2018 (1)
- July 2018 (1)
- June 2018 (1)
- February 2018 (2)
- October 2017 (1)
- September 2017 (2)
- January 2016 (1)
- February 2015 (1)
- January 2015 (1)
- December 2014 (2)
- September 2014 (1)
- February 2014 (1)
- January 2014 (1)
- December 2013 (3)
- October 2013 (1)
- September 2013 (1)
- June 2013 (1)
- January 2013 (1)
Comments (2)